How Can Vision Inspection Ensure Consistent Portion Size & Shape of Meat Products?
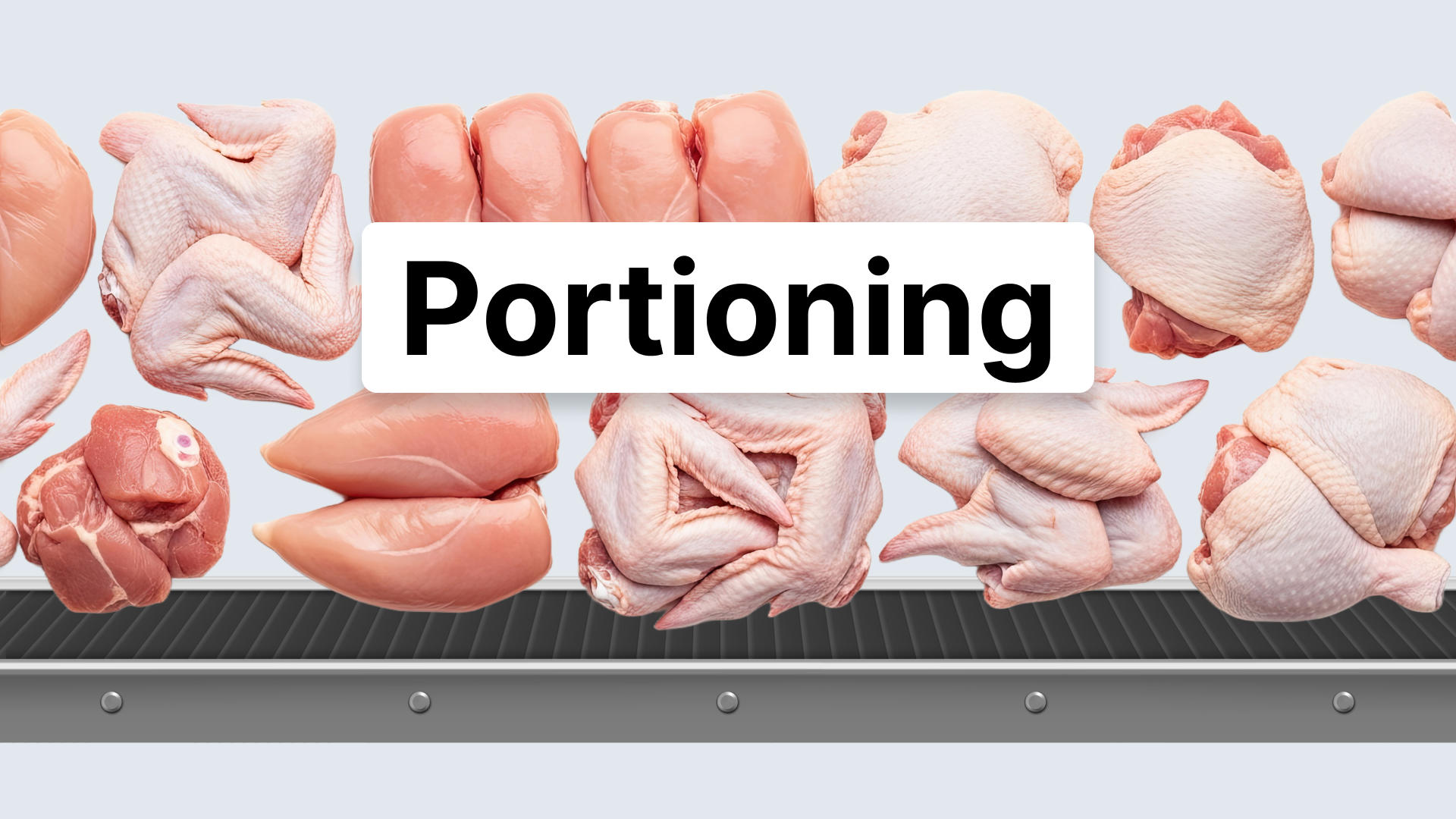
Why is Portion Shape and Size Important in Meat Processing?
There are several reasons why the portion size and shape control of meat products are important:
- Consumer expectations: Customers equate consistency, product uniformity and quality to higher value. Controlled products tend to sell better and lead to higher customer satisfaction.
- Reduced costs: Precise portion control reduces waste and maximizes yield.
- Operational efficiency: Uniform product portions help streamline packaging, reducing time and simplifying inventory.
- Third-party certifications: USDA, AAFC, and EU approvals include portion size and shape into the approval process.
Why are Meat Processors Using Vision Inspection for Product Portion and Shape Control?
Manual product inspection is still the most common method for making these determinations in today’s high-paced processing plants, but presents several challenges for quality control:
- Operator-dependent analysis: Controlling standards from operator to operator or even from the same operator is difficult to maintain.
- Time-consuming analysis: Callipers, scales, colorimeters, and other analog tools to measure products are cumbersome to use.
- Small sample sizes: Sampling a few select products at various intervals does not provide enough information on process performance.
Vision inspection technologies have emerged as trustworthy methods for helping operators measure these quality attributes objectively and at greater speeds (up to 3X faster for one poultry producer). Meat and poultry processors using vision technologies achieve repeatable quality data that is more representative of the production process.
How do Vision Inspection Systems for the Meat and Poultry Industry Work?
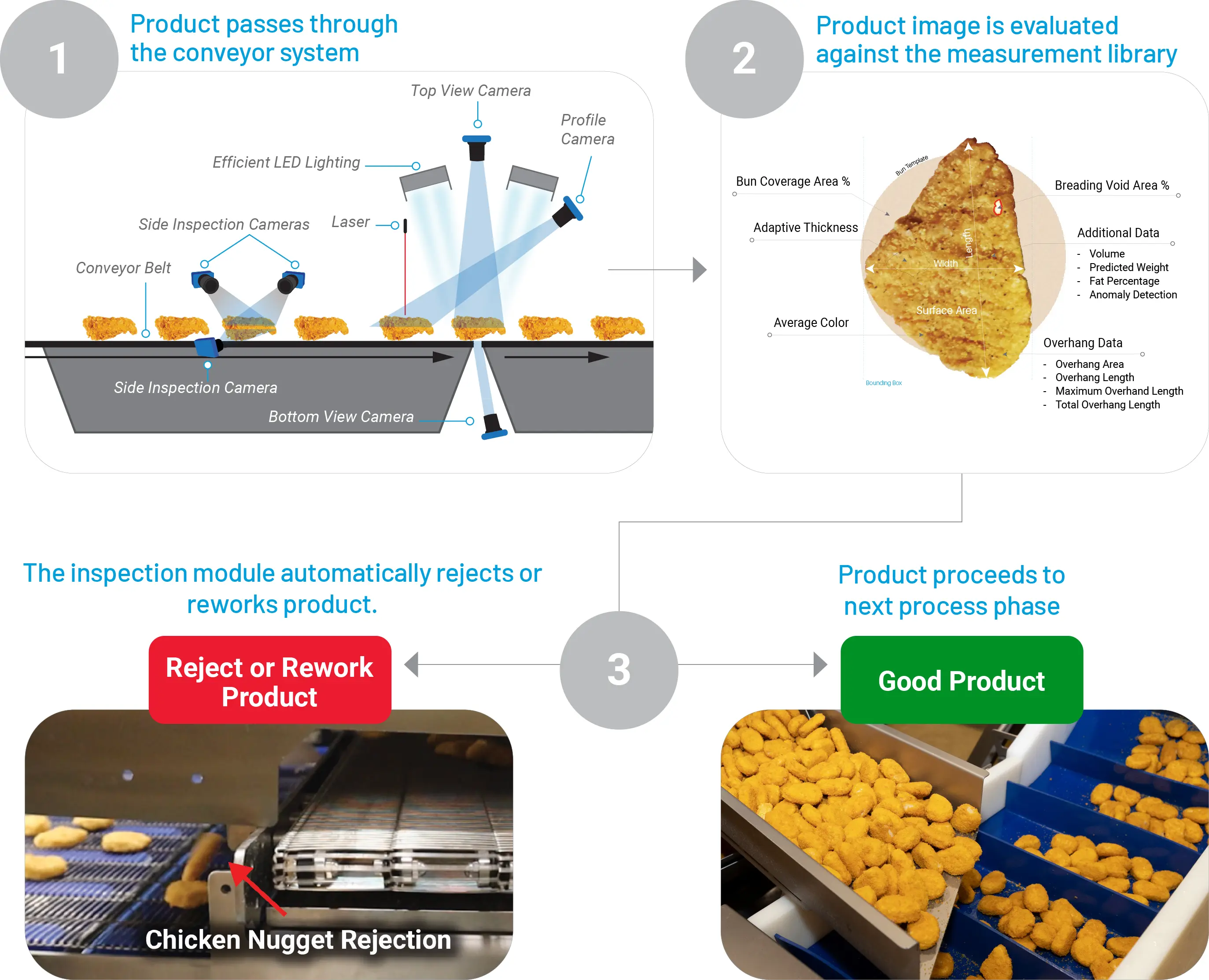
Vision inspection technologies for meat and poultry processors typically consist of the following components:
- 2D/3D Cameras: Capture detailed images from multiple angles, including hard-to-inspect areas like product undersides.
- Specialized Lighting: Reduces glare and enhances product details, ensuring accurate identification (e.g., differentiating marbling from surface shine).
- Analytical Software: Rapidly analyzes images using AI algorithms, accurately measuring size, shape, thickness, fat-to-lean ratio, breading coverage, and color consistency.
How Vision Inspection Analysis Works (step-by-step):
- The system takes real-time images of the products on a conveyor from the top, sides, and bottom of the products (for specific product types).
- The system analyzes images instantly against pre-set quality standards.
- Within milliseconds, the software reports precise measurements, flagging deviations immediately.
- For in-line vision inspection systems, products outside of the acceptable measurement tolerances can be automatically rejected or rerouted for corrective processing.
- All measurements are logged, generating easy-to-understand reports that can be integrated with third-party software like WinSPC, Excel, InfinityQS®, ERP systems, and Freshability®.
What Can Meat and Poultry Vision Inspection Systems Measure?
Vision inspection technologies collect critical measurement data on final products or at various stages of production for quality control, process improvement, product development, and many other applications. Common measurements include:
- 2D-Shape: Length, width, area, symmetry
- 3D-Thickness: Peak thickness, average thickness, center thickness, volume, and predicted weight
- Surface Features: Fat/lean ratio, striations, color, marbling, grill marks
- Defect Detection: Missed breading, blood spots, size deficiencies, and foreign materials
- Weight: Calculated from the vision system or measured by an integrated weigh scale
How Can Vision Inspection Help Control the Size and Portion of Meat Products?
Vision systems instantly identify deviations in portion size and shape, triggering immediate corrective actions to maintain quality and food safety standards. Other benefits for meat and poultry processors include:
- Enhanced manual inspection: An at-line tool like the TheiaVu® WD-300 Vision Measurement System from KPM Analytics combines all manual inspection measurements into a single conveyor pass.
- Immediate detection and correction: With an in-line system like the P-Series Vision Inspection System from KPM Analytics, operators can achieve 100% inspection of products on a conveyor moving at full line speeds.
- Reduction in manual inspection errors: Vision inspection evaluates products using programmed measurement criteria, removing subjectivity from the process.
- Better business decisions: Vision data reveals opportunities to optimize processes across production lines, plants, and facilities.
Boost Efficiency, Profitability, and Consumer Trust with Vision Inspection
Vision inspection for meat and poultry processing streamlines production, ensures compliance, and delivers consistent quality through precise portion measurement and shape assessment. Brands using advanced inspection technology build consumer confidence, capture greater market share, and stay ahead of competitors.
Vision inspection systems can detect a variety of defects, including discoloration, foreign objects, missing pieces, and misshapen products.
Yes, we have interfaced to a variety of systems for real-time data collection and reporting. We also offer real-time process monitoring dashboards.
Yes, we can customize the system based on your line configuration, the type of product you are producing, etc.
Related Blog Posts
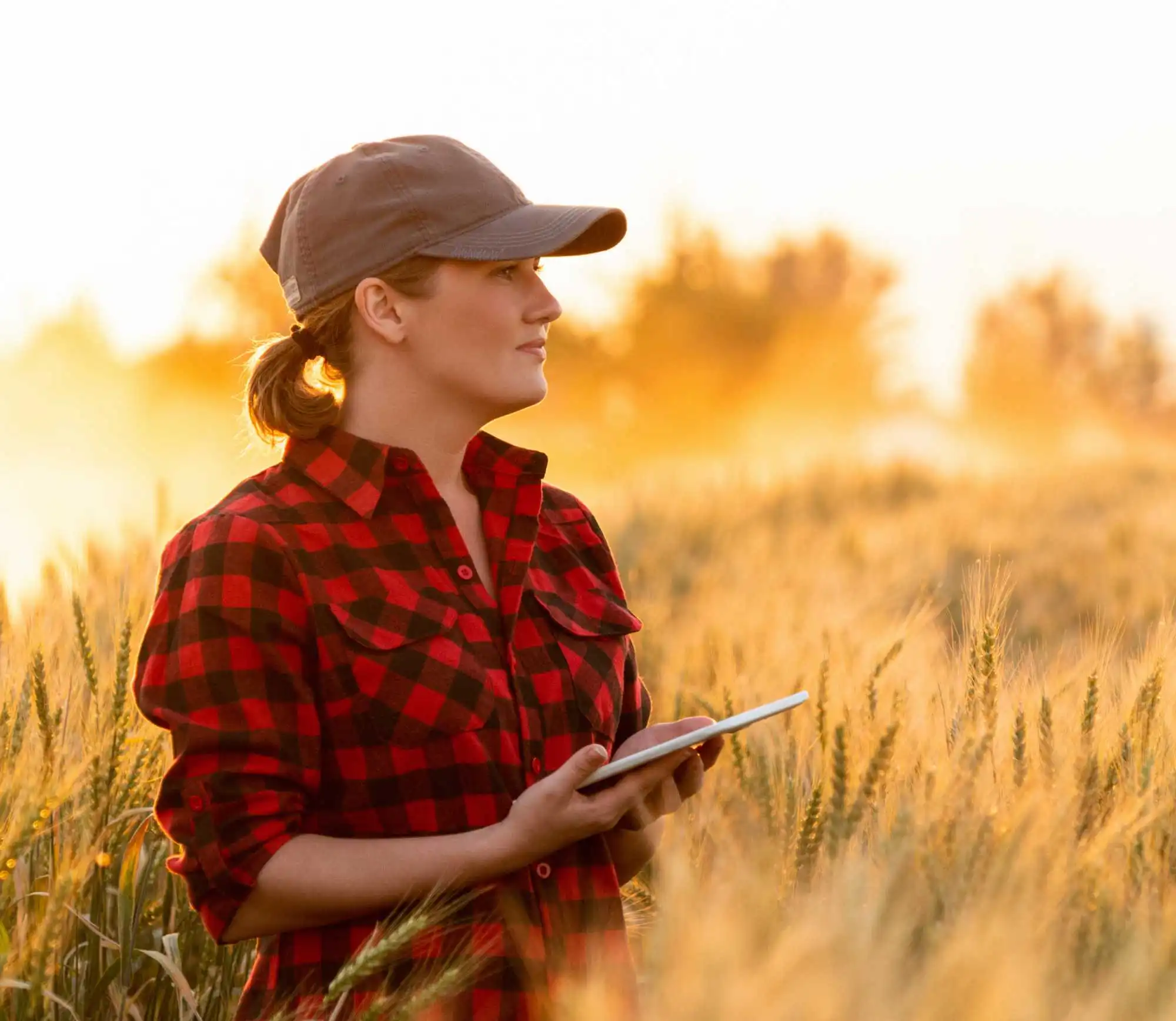
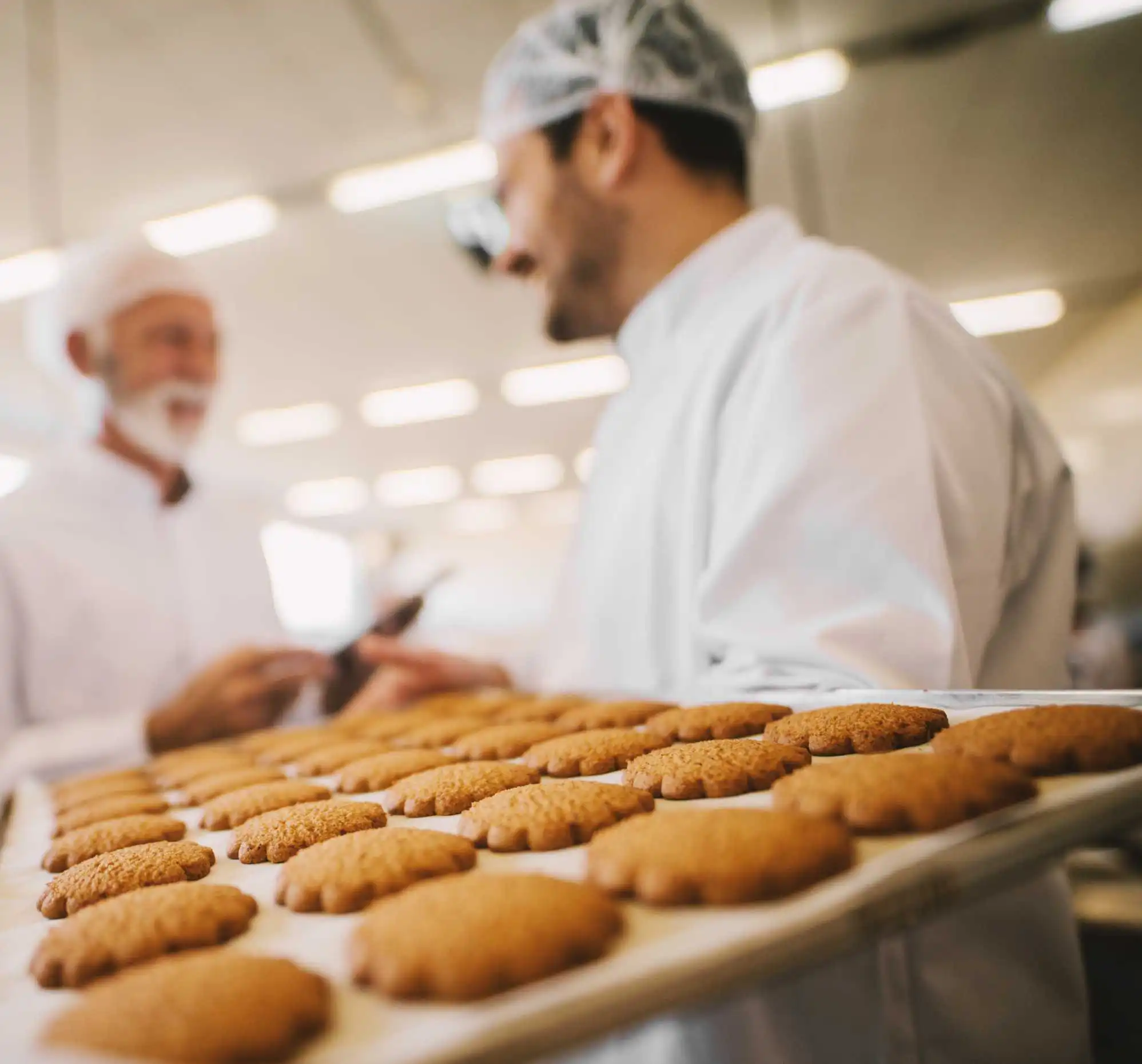
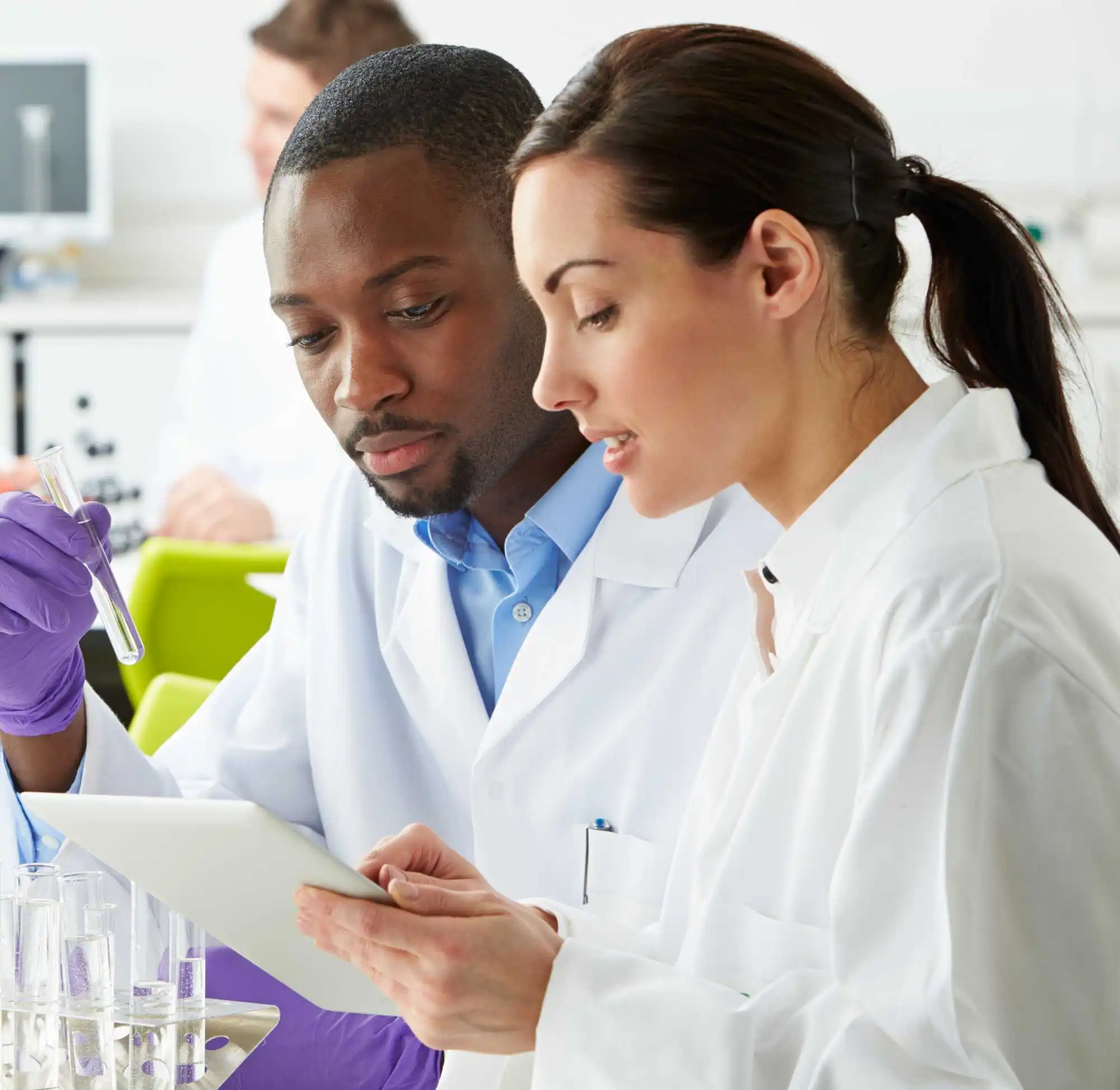
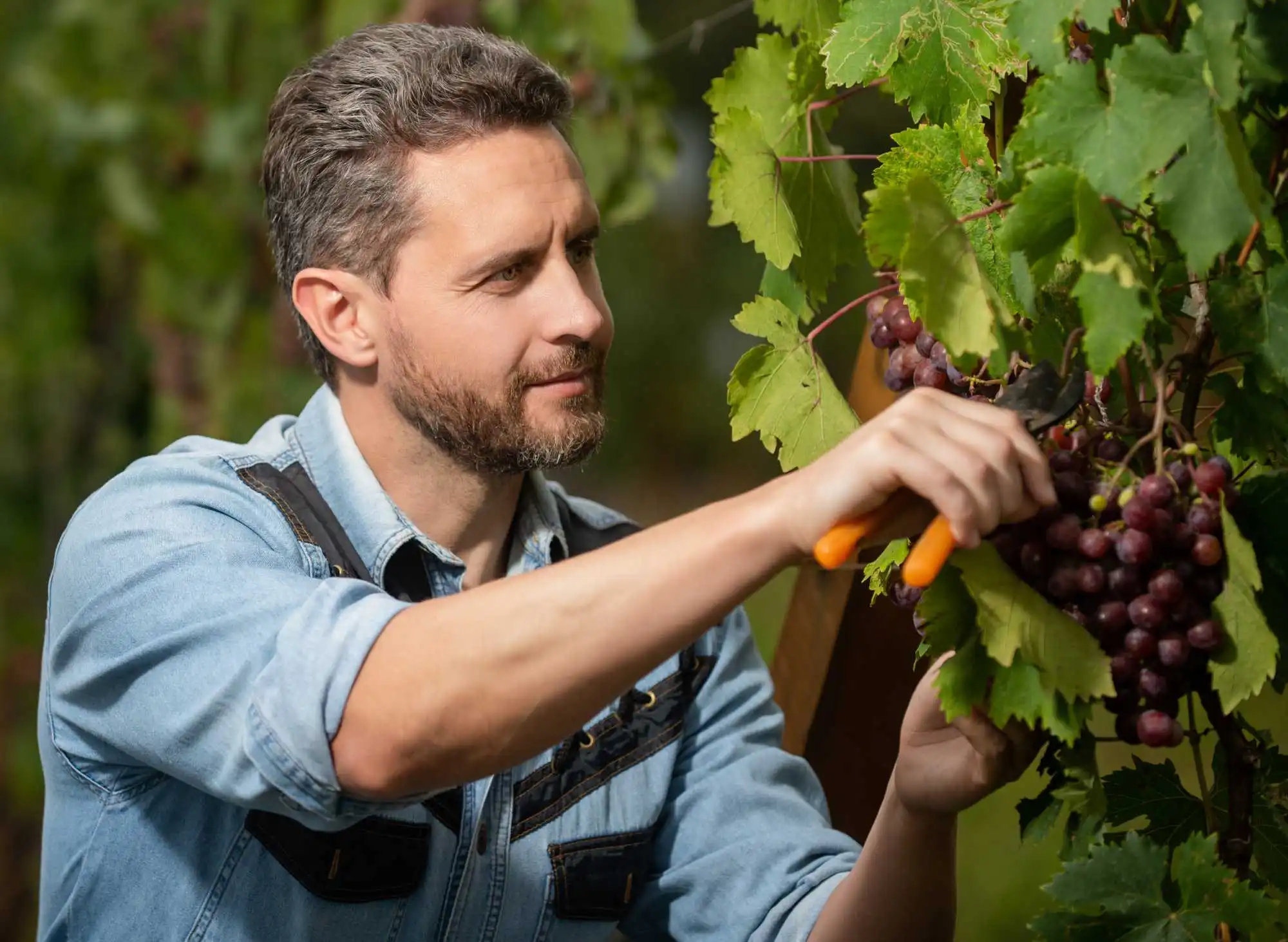