Understanding Foreign Material Risks and Controls in the Beef Deboning Process
.webp)
The Hidden Cost of Missed FM in Beef Processing, And How to Stop It
In beef processing, deboning is a critical step in which carcasses are broken down into boneless subprimals and trimmings. This stage carries a high risk for introducing foreign materials (FM) into the product stream, materials that, if undetected, can compromise food safety, product quality, and regulatory compliance.
Common Foreign Materials Introduced at the Deboning Stage
- Packaging & Shipping Materials: Plastic from liners and crates, pallet wood, cardboard, livestock tags.
- PPE Gear: Tearing of personal protective equipment may introduce rubber, fabric, safety glasses, hairnets, or plastic into the meat.
- Knife & Tool Pieces: Breakage or wear on hand tools and automated cutters can deposit unwanted pieces.
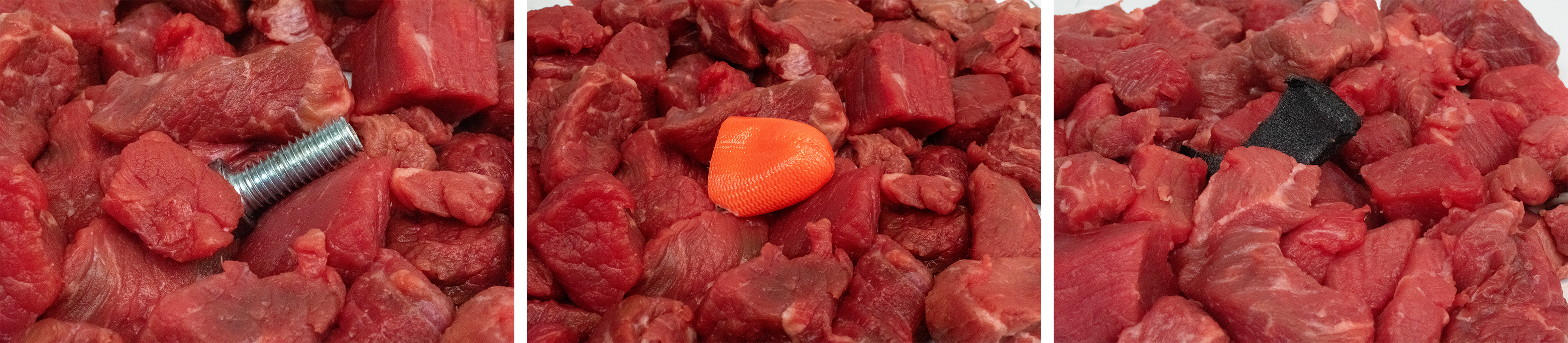
Consequences of Missed Foreign Material
- Equipment Damage: Missing tools, for example, can damage downstream equipment, resulting in costly damage and stalled production.
- Downtime: When FM gets through, the line may need to be stopped to remove the contamination and potentially the product.
- Product Loss: When FM is found, entire lots of product may have to be rejected completely or downgraded to non-human consumption products.
- Consumer Safety Hazards: Hard particles can lead to oral injuries, choking hazards, or consumer complaints. According to the USDA’s Food Safety and Inspection Service (FSIS), such hazards are grounds for product recall (see FSIS Directive 8080.1).
- Brand and Contractual Risk: Even minor FM issues can result in rejected shipments, strained buyer relationships, or loss of premium contracts.
- Regulatory Violations: Under FSIS regulations (9 CFR 417.2), establishments must identify and control hazards reasonably likely to occur, including FM.
Why Foreign Material Is Difficult to Detect Manually
Manual inspection, while still common in some plants, is inherently limited by:
- Staffing challenges like finding and retaining trained or experienced staff
- Human fatigue and inconsistency over long shifts
- Variability in lighting and speed of inspection lines
- Difficulty identifying small, embedded fragments or translucent materials
As a result, many facilities implement vision inspection systems to serve as critical control points. These systems, which include advanced Artificial Intelligence tools, support regulatory compliance and improve detection rates.
Technology’s Role
Vision inspection tools like AI-driven systems can analyze thousands of images per hour and flag contaminants in real time. These systems can:
- Detect both hard and soft contaminants (dense & non dense contaminants)
- Generate image logs for traceability
- Reduce the load on QA inspectors
Advanced AI-based vision systems such as SiftAI® and P-Series are designed to detect a wide range of foreign materials with greater precision and consistency than manual inspection. These systems enhance quality control by providing real-time feedback that fuels effective decision-making to optimize processes. Rather than replacing skilled butchers, vision systems serve as a safeguard, helping to prevent defects from reaching downstream processes or the final product.
Value Across the Operation
- Quality & Safety: Improved traceability, reduced need for rework, data-backed investigations for easier alignment with compliance programs.
- Production Operations: Quick response to process defects reduces waste and maximizes productivity
- Retail/Distribution: Reduced complaints & increased customer satisfaction
General Common-Sense Best Practices
Following common-sense best practices can go a long way to preventing or minimizing contaminants from entering the food supply. Here are a few process control recommendations:
- Root Cause Monitoring: Use daily FM tracking logs to identify common FM types, frequencies, and sources. This data is automatically tracked by vision systems.
- Equipment Checks: Inspect knives, gloves, and conveyors to identify wear or defects. (manual checks)
- Verification Loops: Establish checkpoints between deboning and trimming where FM can be intercepted and removed. (automated vision systems are more efficient here)
- Employee Training: Reinforce the identification and reporting of FM risks during onboarding and refresher sessions.
Resources for Further Reading
- FSIS Directive 8080.1: Recall of Meat and Poultry Products https://www.fsis.usda.gov/policy/fsis-directives/8080.1
- 9 CFR 417.2: Hazard Analysis and Critical Control Point (HACCP) Systems https://www.ecfr.gov/current/title-9/chapter-III/part-417/section-417.2
- CFIA - The Food Safety Enhancement Program approach to a preventive control plan: https://inspection.canada.ca/en/preventive-controls/preventive-control-plans/food-safety-enhancement-program
- European Commission Notice on the implementation of food safety management systems covering Good Hygiene Practices and procedures based on the HACCP principles, including the facilitation/flexibility of the implementation in certain food businesses https://eur-lex.europa.eu/legal-content/EN/TXT/?uri=CELEX%3A52022XC0916%2801%29&qid=1749837240287
The deboning step is one of the most vulnerable points for foreign material entry in beef processing. By combining strong fundamentals, like training and SOPs, with vision inspection for FM detection and traceability, processors can uphold safety, reduce risk, and maintain their customers' trust.
Yes, in most cases we can customize an Over-Line or In-Line system to work with your existing configuration. To be sure, reach out and discuss your ideas with our specialists using the form on our contact page.
Yes, when measuring 100% of all products, a wealth of key production and productivity data such as: throughput/capacity %, defects % , uptime/downtime %, and changeover time.
Yes, we have interfaced to a variety of systems for real-time data collection and reporting. We also offer real-time process monitoring dashboards.
Related Blog Posts
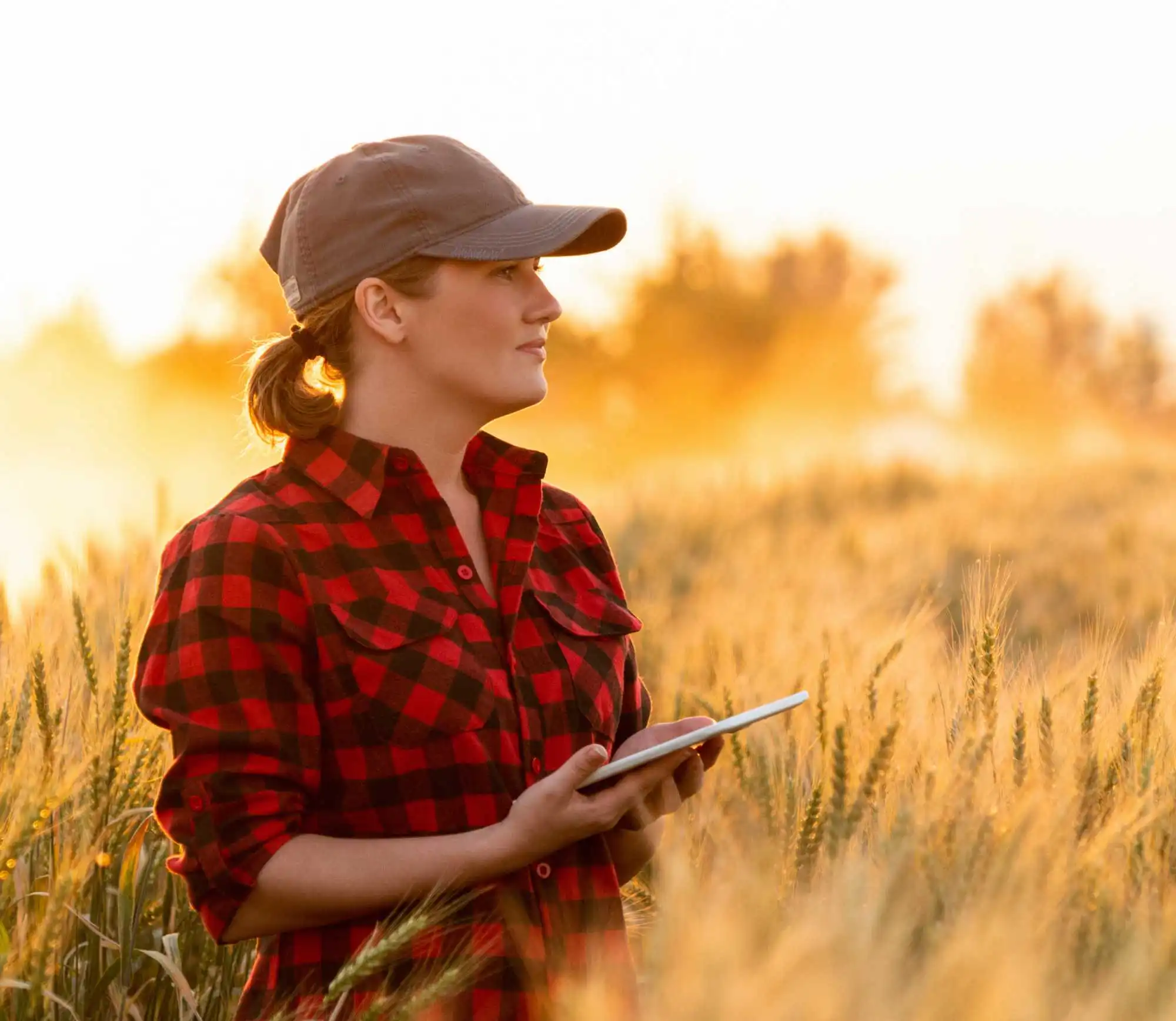
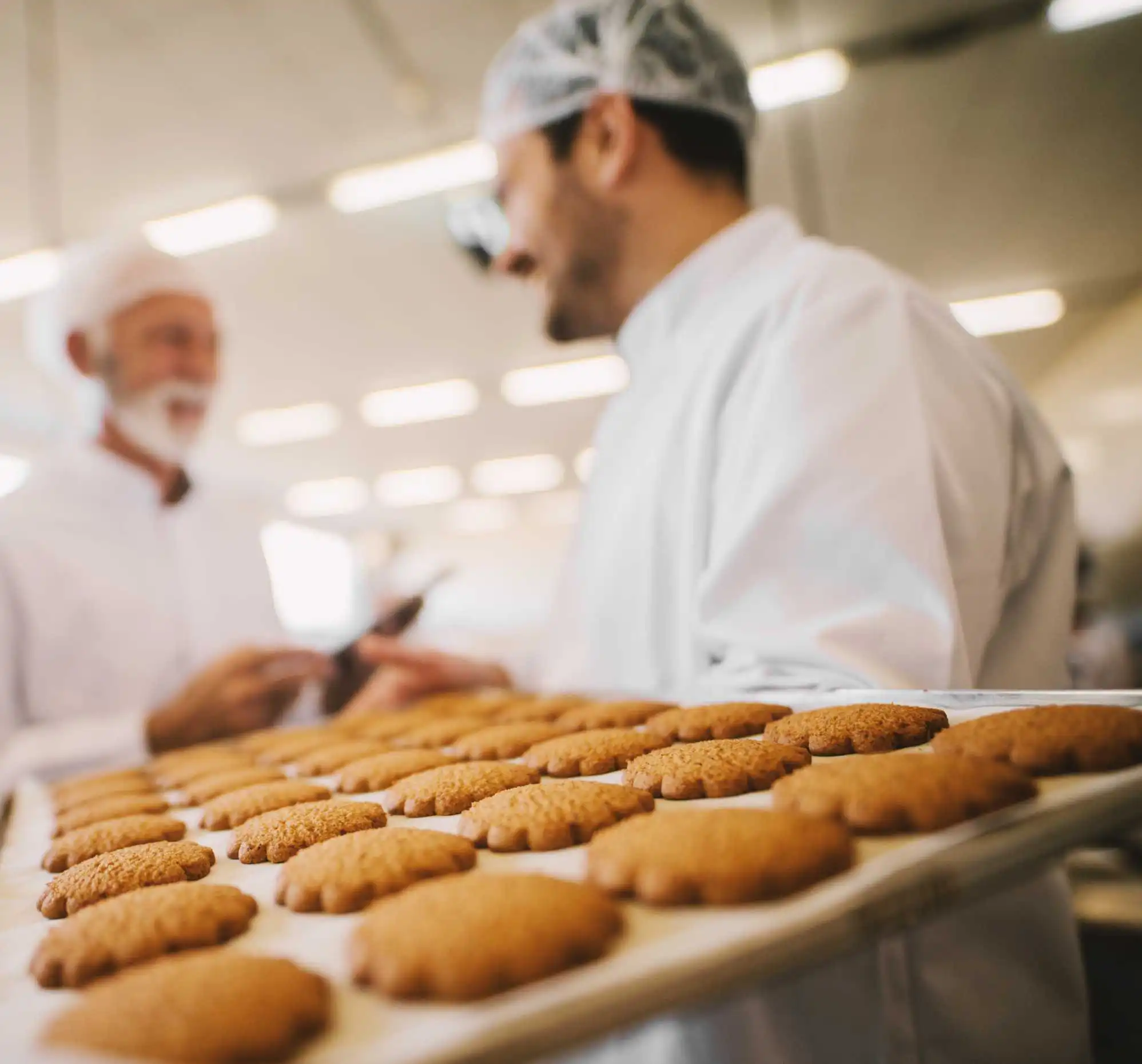
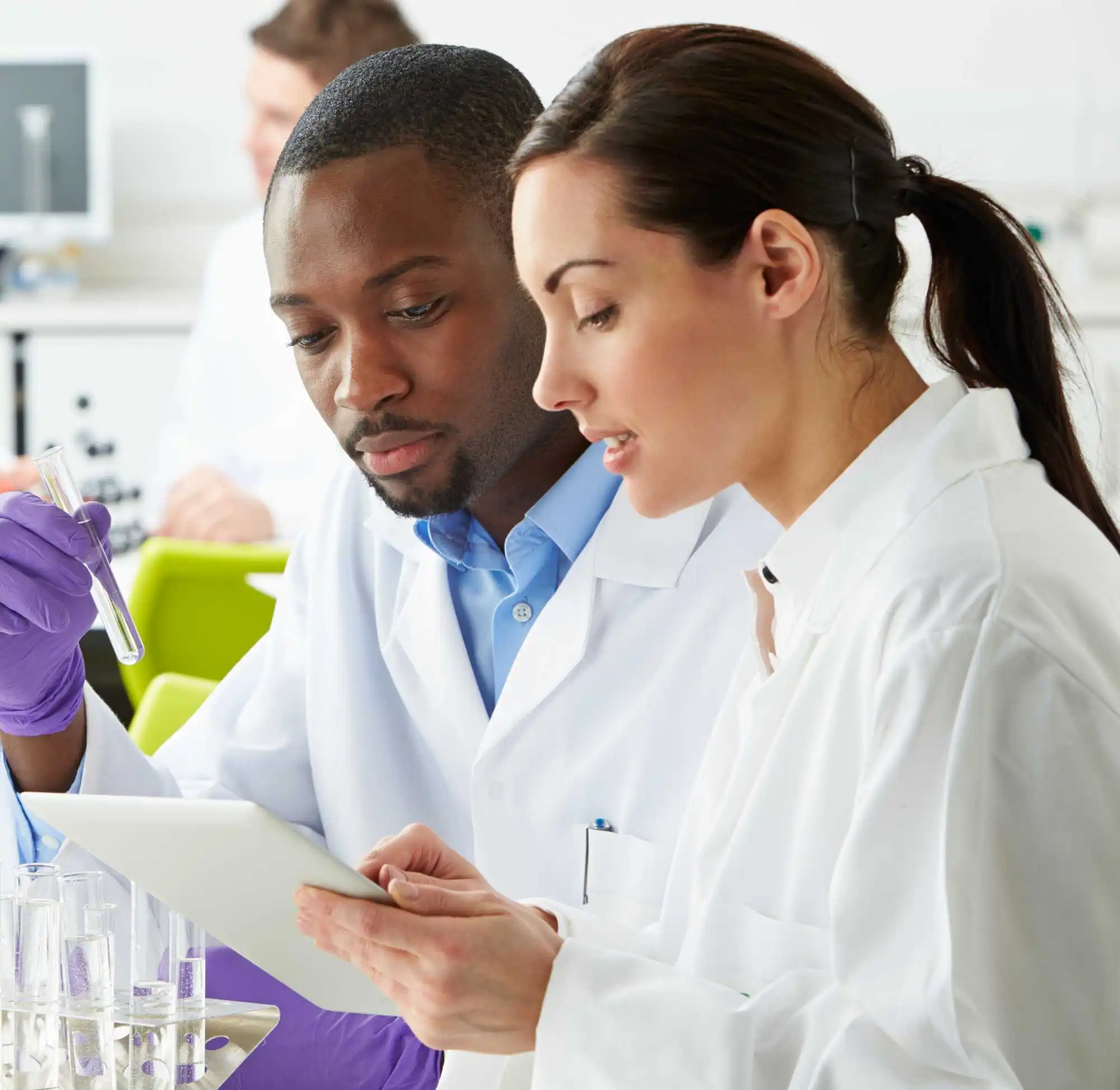
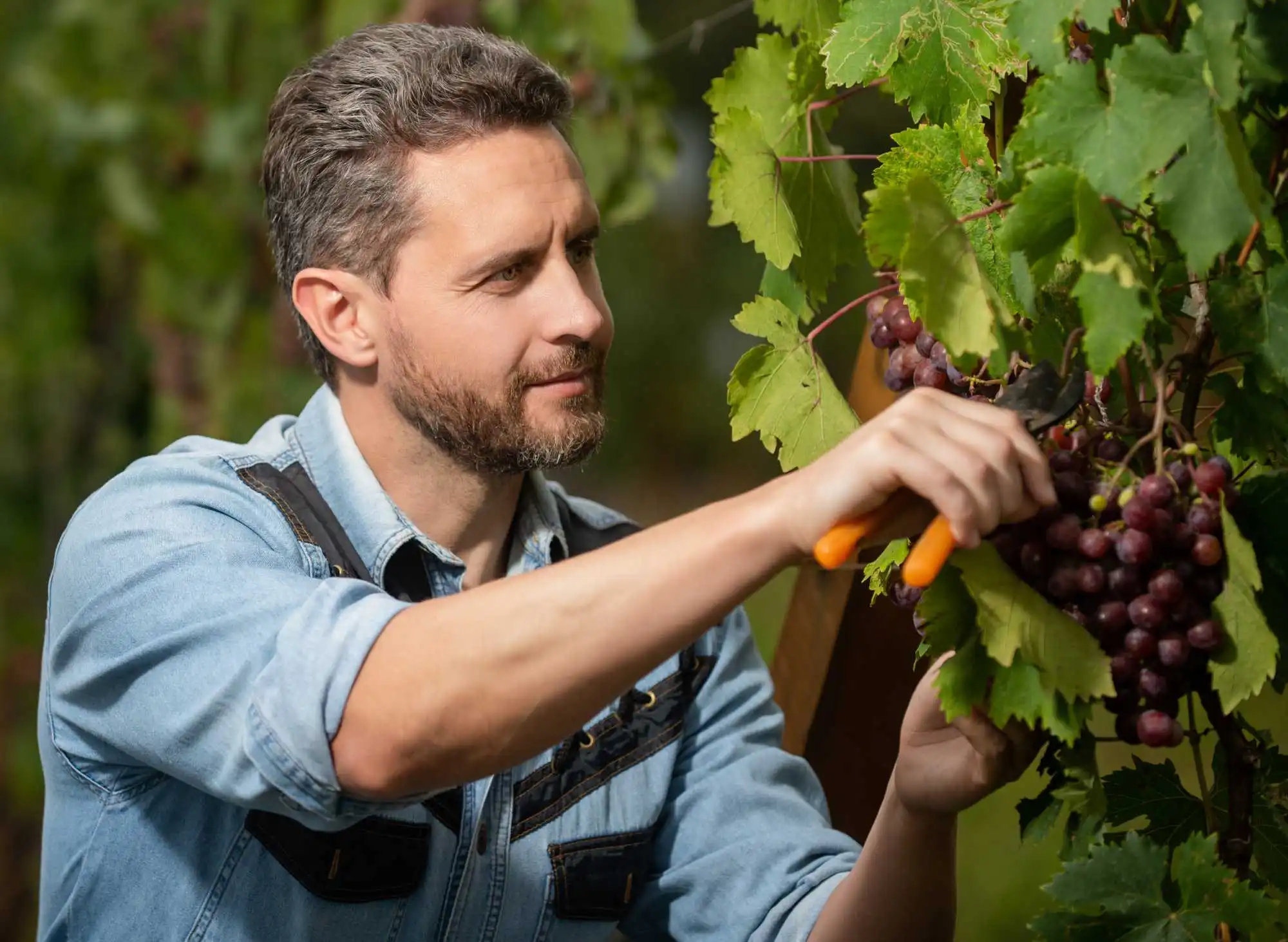